What causes stringing in 3D printing?
Stringing is a very common issue in FDM (fused deposition modeling) printing. It occurs when small strands of molten plastic are left behind between the two points that the extruder travel between.
These strings can be very annoying and can ruin the aesthetic look of your print.
So, how do you solve this problem? Read on to find out!
What is Stringing?
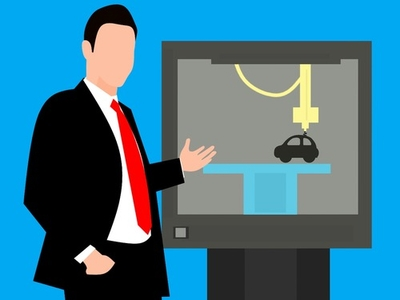
3D printing is an additive manufacturing process that creates a three-dimensional object from a computer-aided design (CAD) model or another digital data source.
The 3D printing process is built layer by layer as the 3D printer extrudes melted filament to create an object.
You might have noticed that some 3D printed objects have “strings” of material connecting different parts of the object.
Stringing, also known as “oozing,” occurs when the molten filament leaks out of the nozzle while the extruder is moving to a new location.
This can happen for a number of reasons, such as a clogged nozzle, incorrect nozzle diameter, incorrect retraction settings, or uneven layer cooling.
Stringing is usually more pronounced with materials that have a higher melt temperature, such as ABS and PLA.
It can also be more pronounced with materials that have a higher viscosity, such as nylons and PETGs.
Read our related article, What is an Extruder in 3D Printing? If you’re new to 3D printing, we discuss extruders, their uses, and types in this guide.
What Causes Stringing in 3d Printing?
One common issue that can occur during 3D printing is stringing.
This happens when small strings of plastic material are left behind between the areas that the printer is supposed to be filling in.
There are a few different factors that can cause stringing:
The filament diameter is too small
This problematic phenomenon occurs when excess material extrudes as a string between two close points on the print surface.
While there are a number of factors that can contribute to stringing, one of the most common causes is an improper filament diameter.
If the diameter of your filament is too small, this may result in insufficient amounts of melted plastic at the tip of your nozzle and significant suction forces pulling air into the nozzle
The extrusion temperature is too low
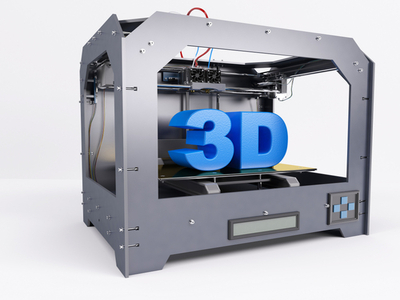
In most cases, stringing is caused by an extrusion temperature that’s too low.
This causes the filament to be less viscous, which results in strings being left behind as the extruder moves between objects.
In some cases, stringing can also be caused by the retraction settings being too high.
This causes the filament to be pulled back into the nozzle too forcefully, which can also result in strings being left behind.
Thankfully, there are a few simple solutions to this problem.
- First, try increasing the extrusion temperature.
- If that doesn’t work, try reducing the retraction amount.
With a little trial and error, you should be able to find the perfect settings for your printer and avoid stringing altogether.
The flow rate is too high
3D printers work by depositing a thin layer of melted plastic onto a build platform.
The plastic is extruded through a small nozzle, and the position of the nozzle is controlled by a stepper motor.
The flow rate of the plastic is regulated by the speed of the stepper motor, and if the flow rate is too high, stringing can occur.
Stringing happens when the plastic cools and hardens before it has a chance to reach the build platform, resulting in long strands of plastic that hang from the nozzle.
In some cases, stringing can be prevented by increasing the temperature of the build platform or by slowing down the speed of the stepper motor.
However, if stringing persists, it may be necessary to adjust the flow rate or to use a different type of plastic filament.
The retraction settings are incorrect
There are several factors that can cause trouble when using a 3D printer.
Stringing can occur when melted plastic extrudes from the nozzle but does not stick to the layer below, resulting in wispy bits of filament that hang off of an object.
In many cases, this problem is due to faulty retraction settings in the printing software.
When these settings are incorrect or insufficient, they can prevent molten plastic from being retracted quickly enough after deposition.
This may also cause excessive oozing and instability in print quality.
What does retraction mean in 3D printing? Learn more about retraction in this handy guide!
Poor ventilation causes the filament to cool too quickly
One of the most frustrating issues that can plague 3D printers is stringing. Stringing can be unsightly, but also can weaken the overall structure of the print.
So, what causes this problem?
One of the most common causes of stringing is also poor ventilation. If the filament cools too quickly, it will contract and start to stick to the nozzle.
Another possible cause is an overly rich lubrication mixture, which can cause the filament to slip out of the nozzle prematurely.
Finally, incorrect retraction settings can lead to stringing, but fortunately, there are a number of ways to combat this problem.
By making sure that the printer is well-ventilated and adjusting the retraction settings, it is often possible to drastically reduce or even eliminate stringing altogether.
Ways to Solve Stringing in 3D Printing
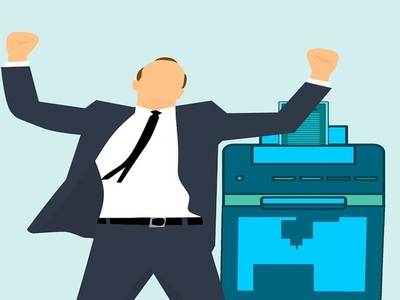
You can solve the problem of stringing by:
- Using a larger nozzle size. This will reduce the amount of plastic that is extruded, and therefore also reduce the number of strings.
- Increasing the temperature of your material. This will make it easier to extrude, and less likely to string.
- Adjusting your retraction settings. This will reduce the amount of plastic that is extruded between moves, and therefore also reduce the number of strings.
- Improving ventilation in your printing environment. This will help to prevent the filament from cooling too quickly and reduce the chances of stringing.
- Using a material that has a higher melting point. This will make it less likely to string.
- Using a material that has a higher viscosity. This will make it less likely to string.
- Using a different printing technique. Some techniques, such as SLA (stereolithography) or SLS (selective laser sintering), are less likely to cause stringing.
- Using a different type of filament. Some filaments, such as PVA (polyvinyl alcohol) or PCL (polycaprolactone), are less likely to string.
Read More: Best Way to Remove Brim From 3D Print. Here’s how to remove prints the RIGHT way!
Conclusion
As you can see, stringing is a common problem, but there are several ways that you can combat this problem, such as by adjusting your retraction settings, improving ventilation, or using a different type of filament.
With a little trial and error, you should be able to find the perfect solution for your needs.
Happy printing!
Read More